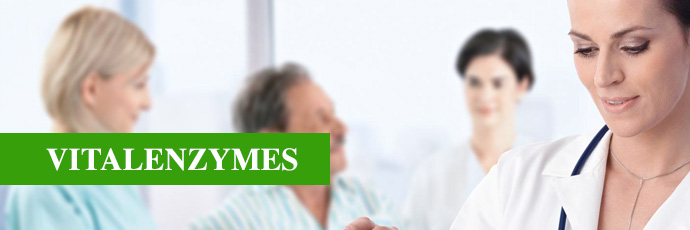
Manufacturing
Certified facility for Large-scale Manufacturing
Our factories have achieved Certified by ISO22000 and HACCP, GMP; HALAL; FDA; with separate buildings for active pharmaceutical ingredient (API) and functional food ingredient. TSIP plant is equipped with 2X50M/T Fermentor, 2X50M/T spare facility for expansion when needed, 4X50M/T Extractor and a series of recovery and purification equipments. Automatic control device is adopted for the production line, so that manpower can be saved and precision controls accomplished.
The Details within a Successful fermentation
The fermentor is capable of full-process control and recording of dissolved oxygen, pH, agitation, temperature, airflow, and pressure application. Eliminating dead volume of sterilization is an important design consideration. Major control valves are diaphragm valves and proportional valves for optimal precision control; high dissolved oxygen demand is also taken into consideration for design of impeller and airflow. With all the details for carrying out a perfect fermentation process, VitalEnzyme considers every detail as an art that needs extreme patience. With this spirit in mind, VitalEnzyme is capable of meeting various demands for different fermentation criteria.
Upon harvesting of fermentation, the concentration of the whole broth before extracting active ingredients is either conducted directly with continuous vacuum evaporator, or by filter press and centrifuge for solid-liquid separation. Finally, proceeding with vacuum drying or frozen drying, pulverizing, up to sieving, filling and packaging, these are accomplished with integrated facilities.
Quality, Hygiene & Safety
The hygiene of the plant and the facility determine the manufacture quality. Between different lots of raw materials on the production line, the sanitary and hygiene is very important for maintaining the purity and quality of the products. To ensure compliance with VitalGroup’s standards, bodies of all the reactors in the plant are made of SUS316L stainless steel, with 400 mesh polish for the tank internals, for facilitating cleaning process and avoiding residuals of remainders on the surface. Finally, the downstream recovery and purification segmentation is installed with explosive-proof grade equipment to ensure safety, and further adds value to the plant.